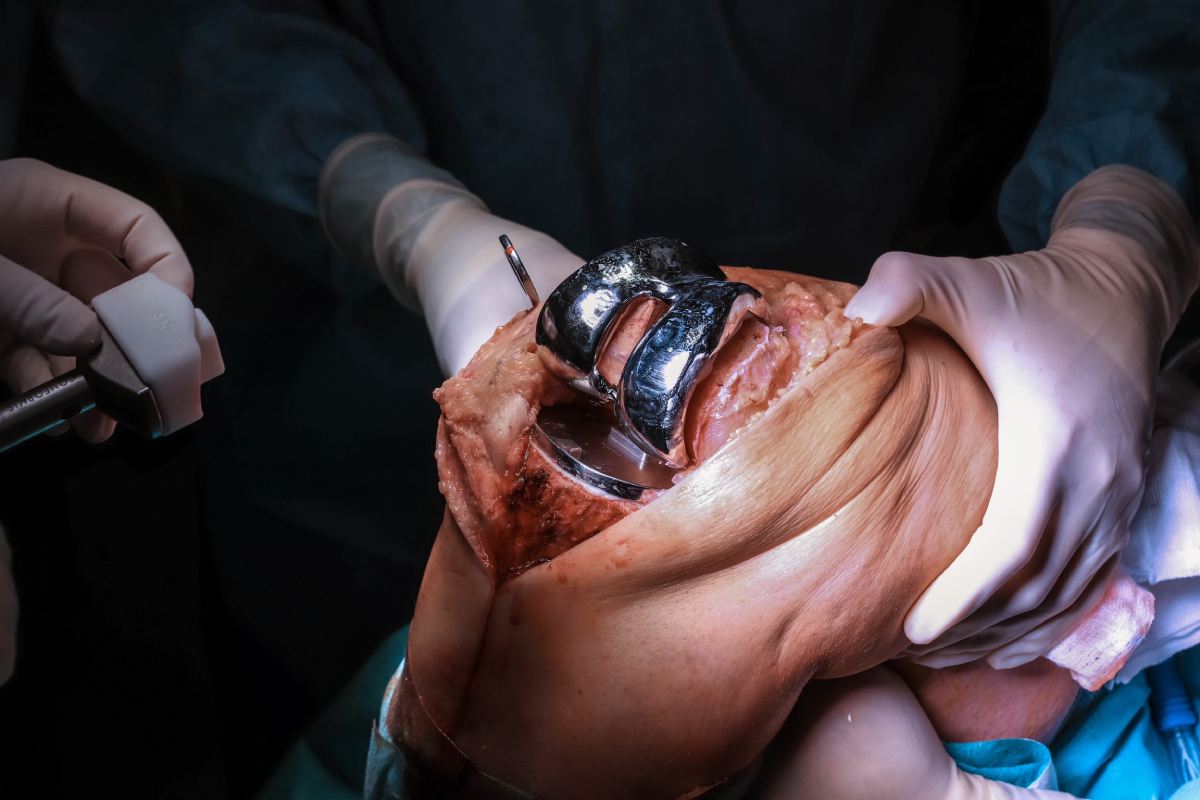
La cirugía ortopédica y traumatológica ha dado un nuevo paso al frente al pasar de las protésis de rodilla ‘a medida’ a las personalizadas para la articulación de cada paciente, según Fernando Sanz Zapata, jefe de la Unidad de Rodilla de la Clínica Cemtro, de Madrid, cuyo equipo ha utilizado la tecnología de impresión 3D en metal para implantar una protésis que imita la anatomía de la forma de la rodilla del paciente. Este equipo ha implantado en su centro la primera protésis de estas características y, en breve, realizarán dos más.
Sanz explica a DM que, en condiciones normales, las prótesis de rodilla cuentan con modelos estandarizados, con un número reducido de tallas para los elementos femoral y tibial, que se van adaptando a la anatomía del paciente. Ahora, la prótesis se fabrica específicamente para cada paciente con tecnología tridimensional.
Aspectos novedosos
La novedad de este abordaje radica en que “a pesar de los avances técnicos de los modelos actuales, sigue habiendo hasta un 20% de pacientes operados de prótesis total de rodilla (PTR) que no notan la rodilla como suya. Aunque reconocen que la cirugía les ha mejorado mucho y les permite más actividad física que antes, la satisfacción no es total, a pesar de la adecuada rehabilitación, tener buena movilidad y ausencia de dolor. Por ello, se ha recurrido a sistemas más novedosos y menos diversificados que, aunque más costosos, generan ventajas destacables: además de una mayor satisfacción, se presupone que es más duradera que los modelos habituales porque es una resuperficialización de su rodilla”. En este sentido, el cirujano señala que la supervivencia de los implantes estándar es de entre el 85-90% a 15 años.
Un 20% de personas con prótesis total de rodilla no está totalmente satisfecho con los implantes convencionales
La prótesis, desarrollada por ConforMIS y comercializada por la empresa Medcomtech, se personaliza mediante una planificación preoperatoria basada en un estudio de imagen por TAC que permite una reconstrucción tridimensional exacta de la articulación del paciente y cuyos datos se envían a la factoría encargada de fabricar las prótesis. Desde allí, el ingeniero mecánico traza un plan que se reenvía a los cirujanos que, de forma consensuada, pueden modificar ligeramente los ejes si se considera más adecuado para la cirugía del paciente.
“El proceso tarda alrededor de cinco semanas hasta que llega la prótesis fabricada en 3D. Además, los cortes que tenemos que hacer para colocar los implantes se realizan mediante unas guías específicas de navegación, a modo de negativos de la rodilla del paciente que encajan como un guante en la mano y permiten una precisión mayor que con la técnica habitual”, detalla Sanz.
Indicaciones y manejo quirúrgico
Entre las indicaciones para acceder a este tipo de prótesis personalizadas se encuentra que sean ‘rodillas vírgenes’ en las que se va a implantar una prótesis primaria –no para una revisión protésica- y que no exista una anatomía no distorsionada porque pueden reproducirse las condiciones que han llevado al paciente, por ejemplo, a la artrosis.
En cuanto a la edad, el cirujano indica que se encuentra en la que está establecida para el estándar de prótesis, aunque “lógicamente, cuanto más joven es el paciente, mejores resultados se pueden obtener”.
La técnica quirúrgica es la misma que se emplea para el implante de prótesis convencionales, aunque el cirujano subraya que, en teoría, existen ciertas ventajas: no es necesario llevar a cabo tanta disección porque las medidas están muy ajustadas y, además, no se emplean las guías habituales de alienamiento porque se dispone de guías navegadas.
“Al no tener que abrir la cavidad medular de los huesos, existe menos sangrado que, quirúrgicamente, entraña menos complicaciones peri y postoperatorias. La rehabilitación y recuperación no varían, aunque se sugiere que si el sangrado y el dolor, entre otros factores, es menor, la rehabilitación comenzará antes. Aunque se trata de elementos subjetivos que tendremos que ir analizando a medida que las series de implantes sean más largas".
Se sugiere también otra posible ventaja relacionada con la fricción de las partículas protésicas y es que como se recrea la anatomía del paciente, ya que es una copia exacta de su rodilla antes de haberse desgastado, la tensión ligamentosa es la que ha tenido siempre y no se peca, por ejemplo, de dejar la prótesis más apretada de un lado que de otro o de ‘engañarla’ soltando los ligamentos. En teoría, si los ligamentos están equilibrados, el polietileno no se desgasta más en un sitio que en otro”.
via Noticias de diariomedico.... https://ift.tt/3jzxROt
No hay comentarios:
Publicar un comentario